Compact Wireless Temperature, Vibration and Movement Sensor
SmartBUG®
Temperature Detection
Vibration Analysis
Gyroscope
Long Life
Asset Health Alerts
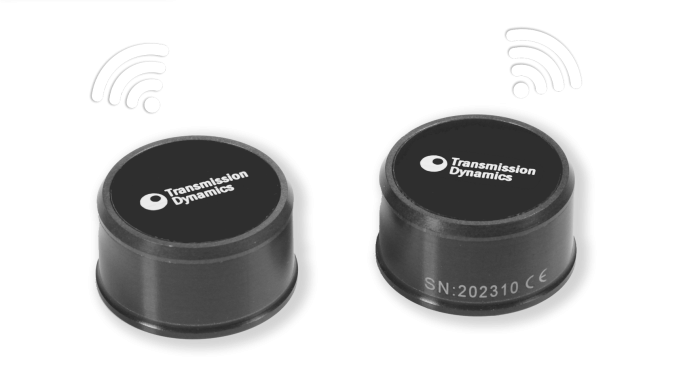
Key Features of SmartBug® Wireless Sensors
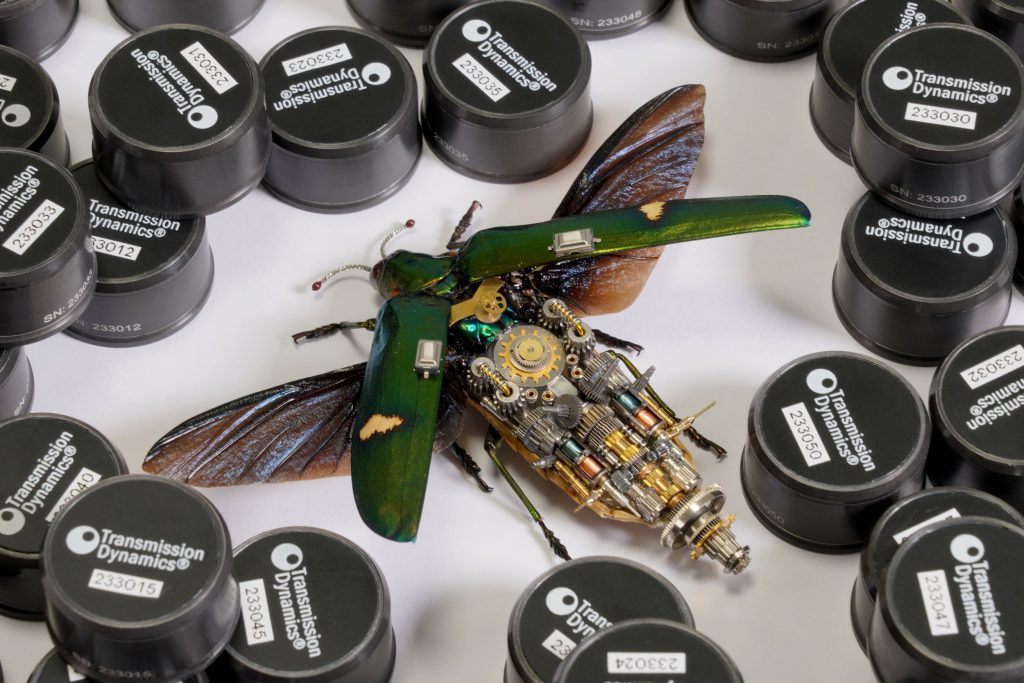
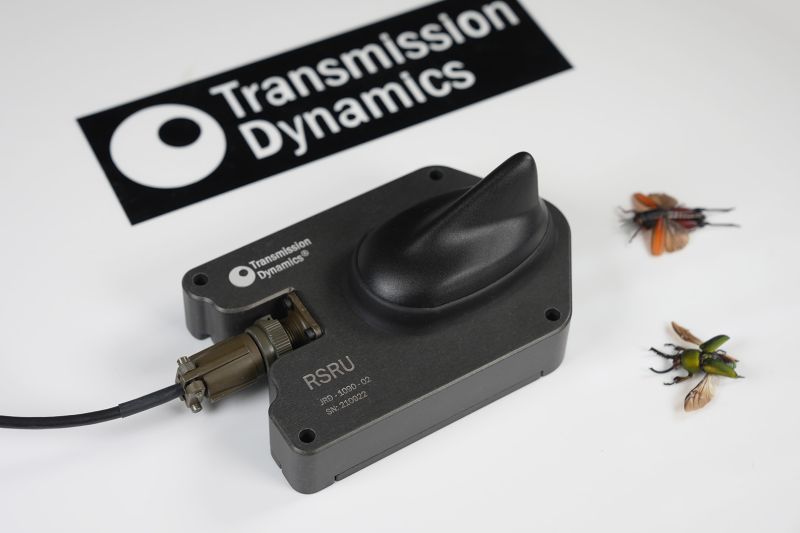
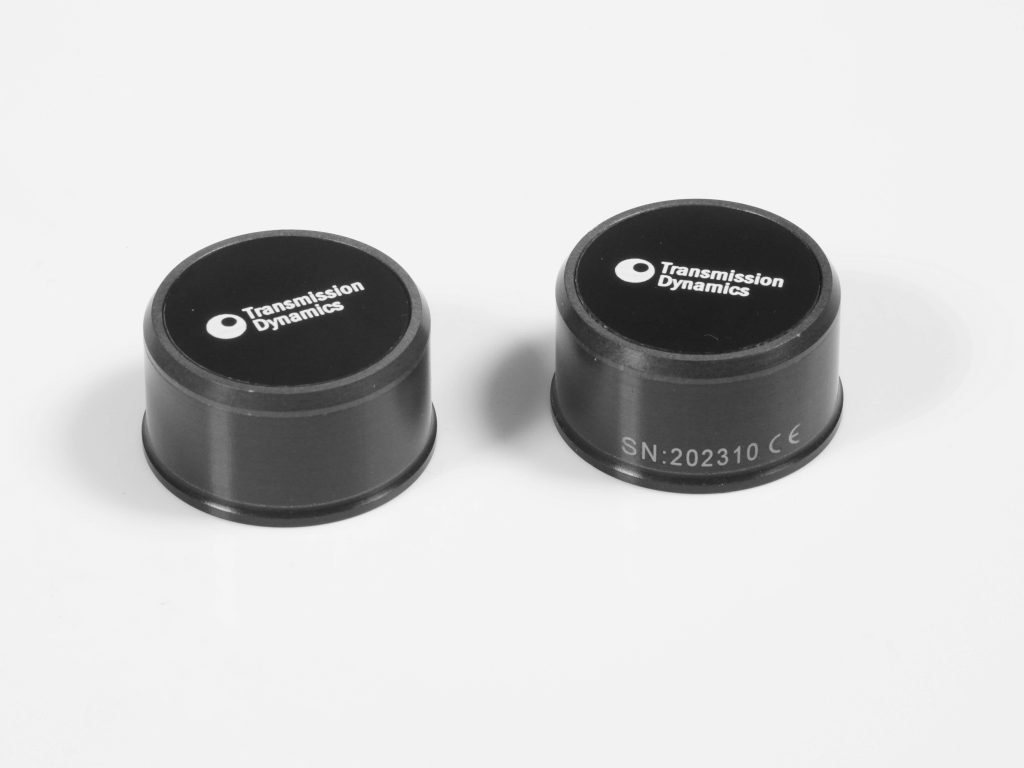
Triaxial Accelerometer
The SmartBug® is equipped with a triaxial accelerometer, which means it can measure acceleration in three perpendicular directions. This capability is crucial for monitoring the movement and vibrations of industrial assets such as machinery, vehicles, or infrastructure. It provides a comprehensive view of how these assets are performing in real-time. ± 16 g or ± 200 g triaxial acceleration measurements, at up to 6,400 Hz per channel.
Triaxial Gyroscope
The triaxial gyroscope feature provides precise measurements of rotational movements in three dimensions, enabling comprehensive motion analysis and enhancing the product's versatility.
Compact Miniature Size
One of the standout features of the SmartBug® is its compact size. Measuring only 27mm in diameter and 18mm in height, it can be easily installed in various applications without taking up much space. The versatility of our compact wireless sensor allows it to fit into tight spaces where larger wireless temperature & vibration sensors might not be practical.
Robust, Rail-Approved Design
The SmartBug® is designed to operate in demanding environments with high levels of vibration. Its robust wireless vibration sensor construction ensures it can withstand the rigors of industrial use. Additionally, it has received rail approval, making it suitable for deployment in the railway industry where vibrations are common.
Wireless Connectivity for Simplicity
SmartBugs® eliminate the need for cumbersome wires and cables. They communicate wirelessly over short-range radio (up to 50 m), simplifying installation and reducing the clutter associated with traditional wired sensor systems.
Simple Installation
Installing SmartBugs® is a straightforward process. They can be securely bonded to the target surface using structural adhesive. This simplicity means that the sensors can be up and running in a matter of minutes, minimising downtime during installation.
Long Battery Life
The SmartBug® is designed for long-term use. Its internal battery can typically last up to three years, reducing the need for frequent battery replacements. Furthermore, the intelligent sleep capacity helps conserve battery life, ensuring extended operational longevity.
Zero Maintenance
Once installed, SmartBugs® require minimal maintenance. Their robust design, long-lasting battery, and wireless communication reduce the need for regular upkeep. This "set it and forget it" approach to monitoring simplifies ongoing management and keeps maintenance costs low.
How the SmartBug® Data Flow works
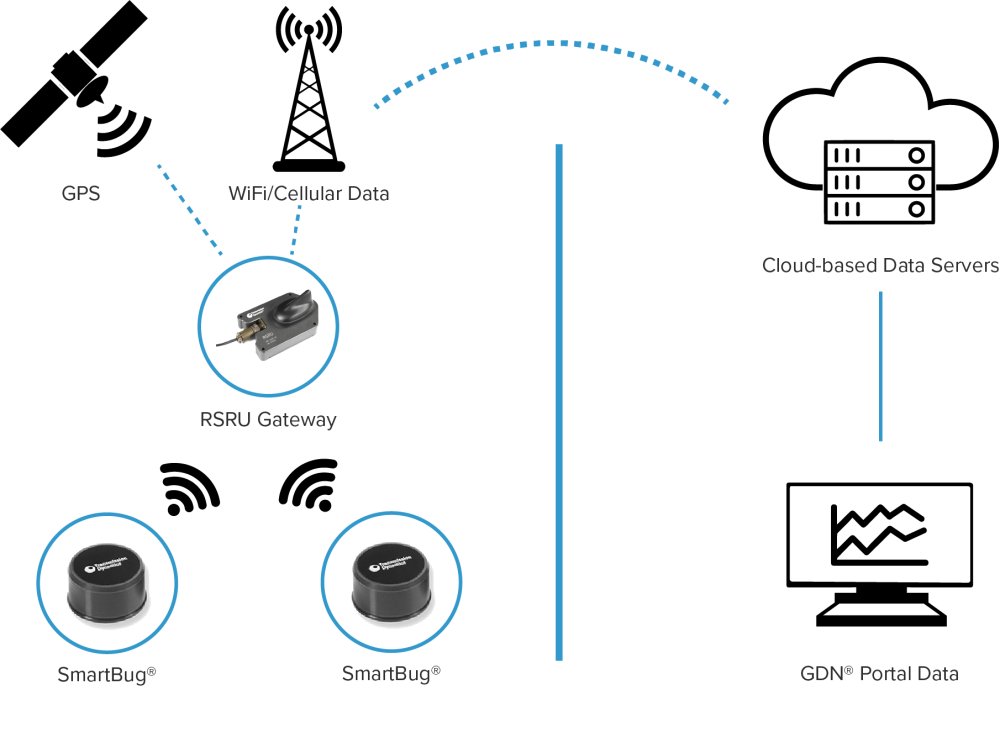
How SmartBug® wireless temperature & vibration sensors are utilised in optimising industry.
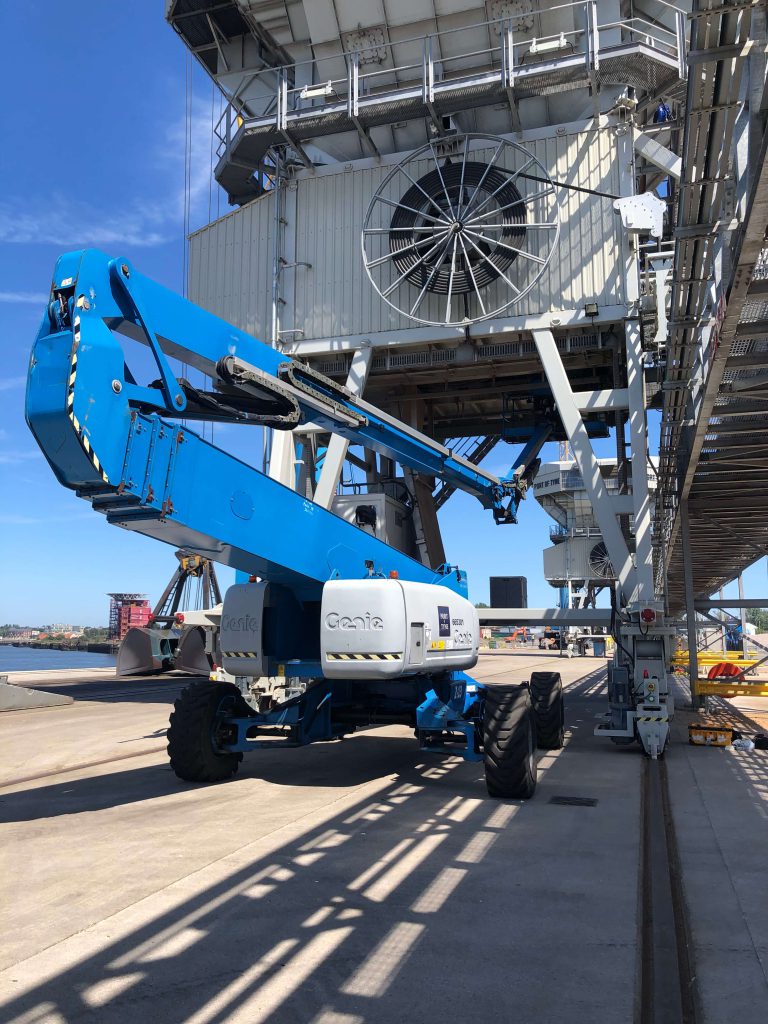
Ports
The SmartBug® is strategically placed on cranes, container handling equipment, and dock structures in ports to monitor vibrations, strains, and temperature. This data ensures the structural integrity of critical infrastructure and helps optimise equipment maintenance schedules, reducing downtime and enhancing the efficiency of port operations.
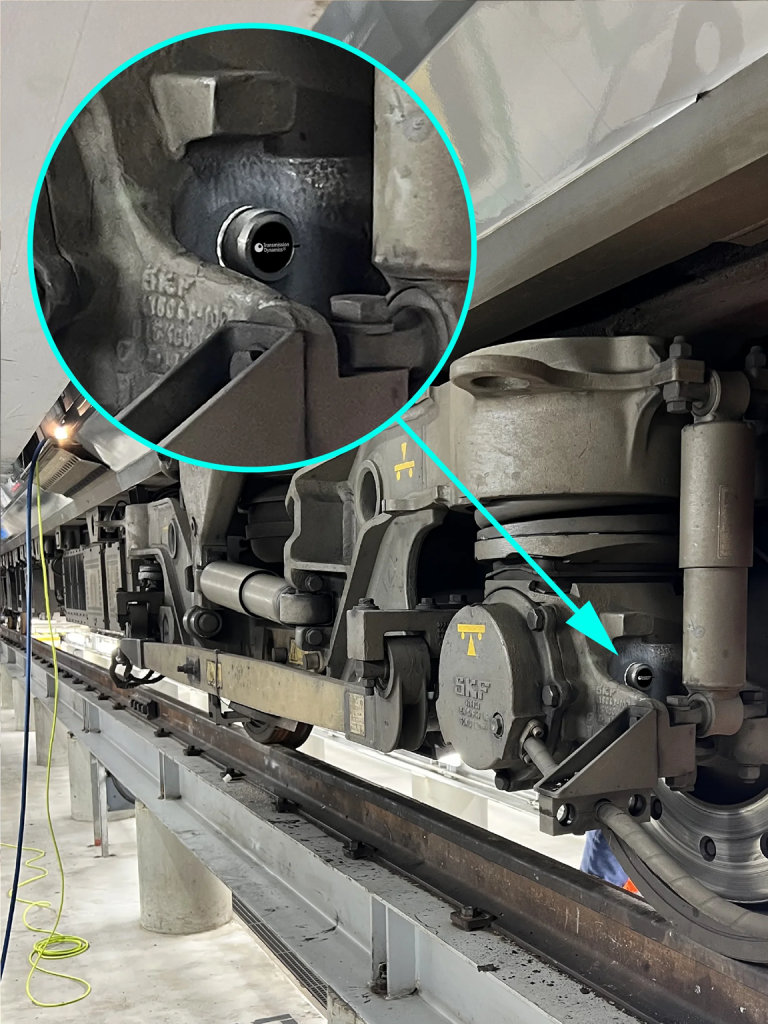
Rail
In the rail industry, SmartBugs® are attached to locomotives, freight cars, and tracks to track vibrations, strains, and temperature variations. This real-time data aids in predictive maintenance, allowing rail operators to identify potential issues before they become critical. It also helps improve the safety and reliability of rail transportation systems.
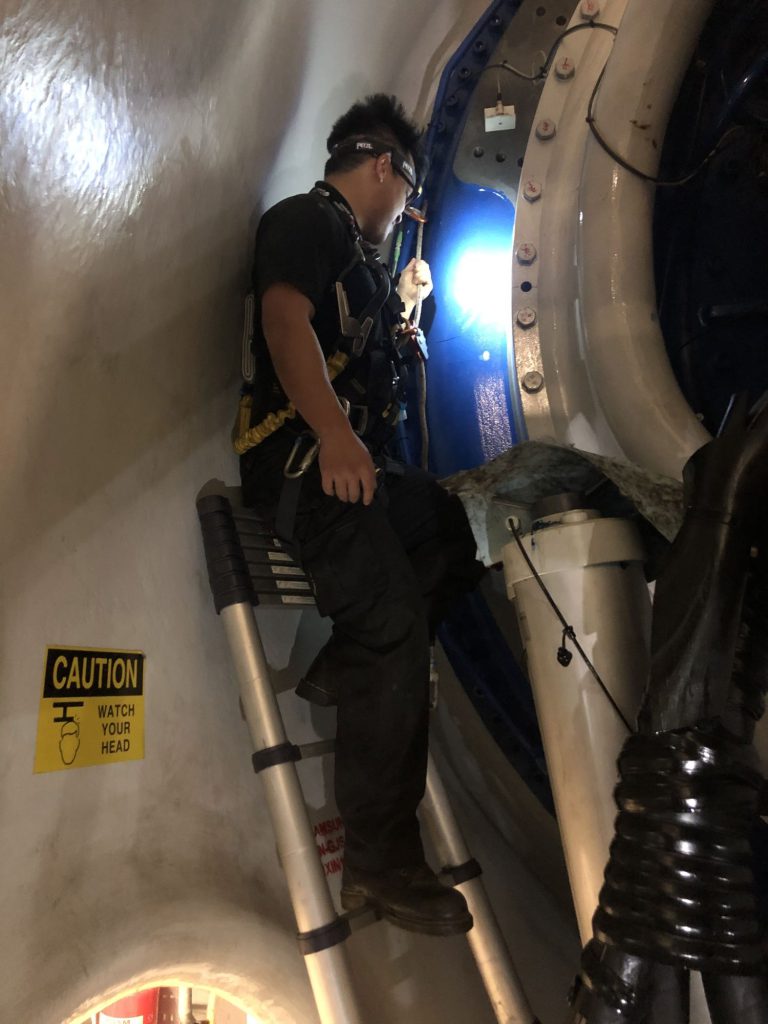
Power Generation
In wind power generation, SmartBugs® are affixed to wind turbine components to monitor strain, vibration, and temperature, enabling proactive maintenance and maximising energy production efficiency.
Periodic Sampling
Adjustable to desired sensitivity and levels
User Adjustable
Sampling Frequency, Duration & Wake Interval
Edge Processing
Real-time data analysis & decision-making at the source.
Remotely Configurable Settings
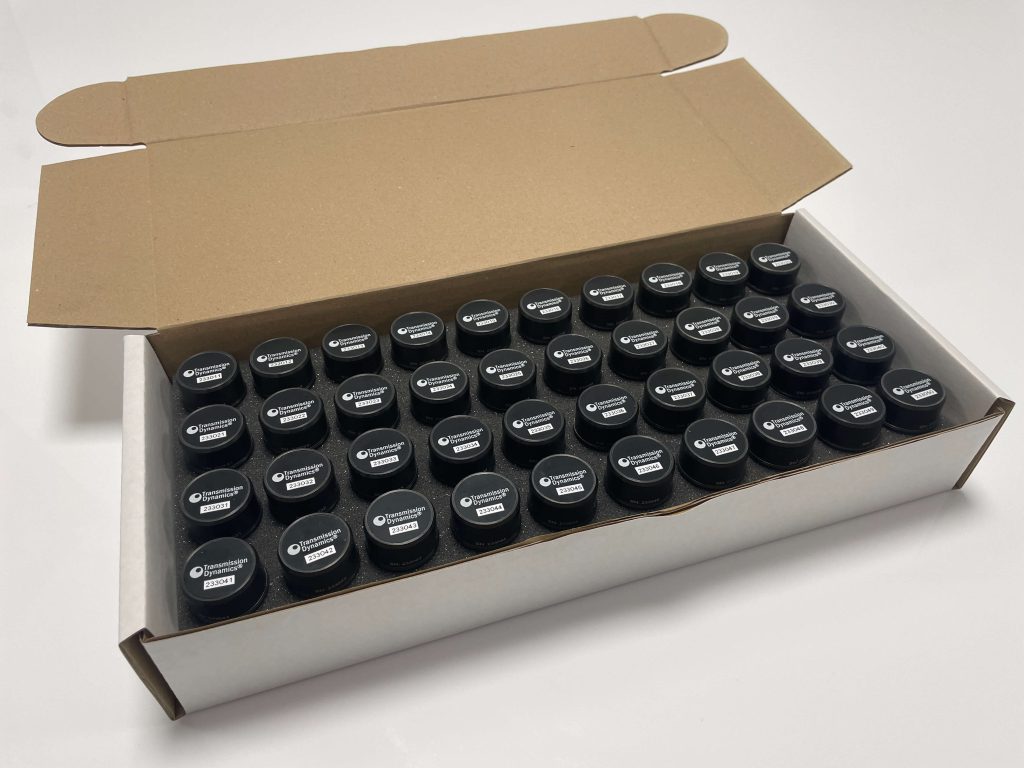
API Access
Real-time access via simple API (Application Programming Interface)
TRIGGERS
Adjustable RMS and peak-to-peak triggers
Benefits of using SmartBug® wireless sensors
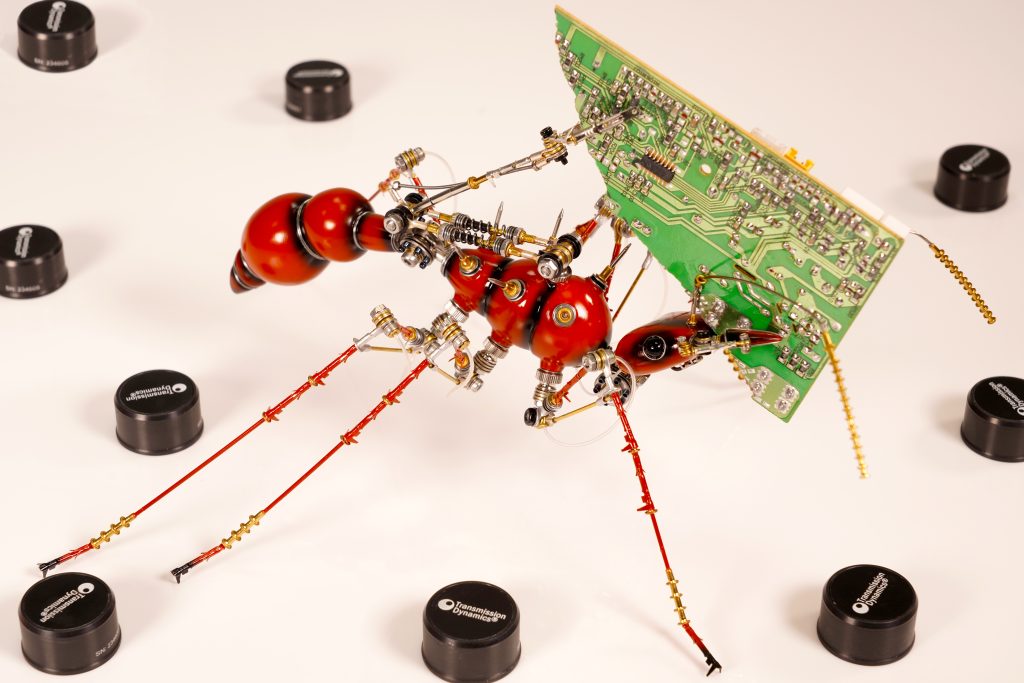
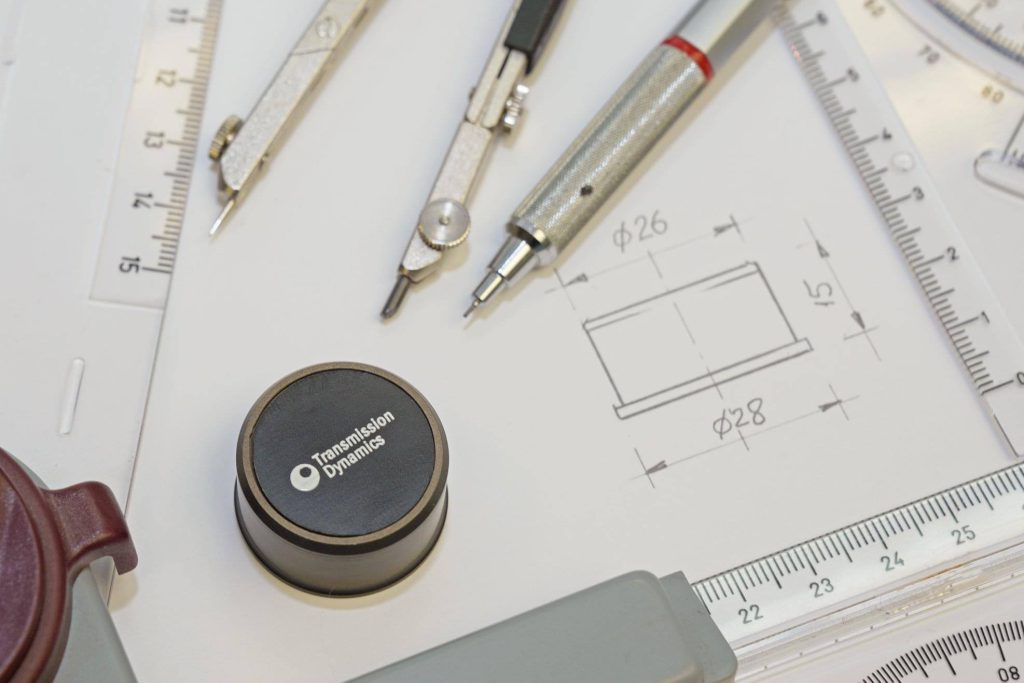
Increase Maintenance Efficiency
By adopting our solution, you can significantly enhance maintenance operations, streamlining processes and maximising resource utilisation for improved overall efficiency.
Wireless, Sensor-Based Solution
Our innovation utilises wireless temperature & vibration sensor technology and advanced wireless movement sensors to provide a cutting-edge solution. It enables real-time monitoring and analysis of gearbox health, offering you crucial insights into performance and potential issues.
Extend Maintenance Intervals
With our technology, you can extend maintenance intervals without compromising on operational safety. Continuous monitoring allows for predictive maintenance, reducing unnecessary downtime and costs associated with premature overhauls.
Rail Standards Compliant
The SmartBug® technology is fully rail compliant. Our products are fully tested and are both EMC Tested and IP 68 rated.
General Detection
Rail-Specific Detection
Bearing Issues
SmartBugs® can detect early signs of bearing issues by monitoring vibrations and temperature variations. Sudden increases in vibration levels or temperature can indicate potential bearing failures, allowing for timely maintenance to prevent costly downtime.
Wear of gearbox components such as gears and bearings can cause an increase in noise and vibration, and lead to premature failure of the drive-train.
Our SmartBug technology identifies early gearbox issues; the pictured example exceeded fleet average vibrations, prompting client inspection and repair.
Out Of Balance
SmartBugs® can detect out-of-balance conditions by analysing vibration data. Any deviations from the normal vibration signature can indicate imbalance issues, allowing for adjustments to be made to prevent further damage or wear.
Duty Cycle
SmartBugs® provide insights into the duty cycle of equipment by monitoring strain, vibration, and temperature changes during operation. This data helps in optimising maintenance schedules and ensuring that equipment is used within its designed duty cycle, increasing its lifespan.
Wheel flats are localised flat spots on train wheels caused by prolonged skidding, leading to increased vibration, noise, and track damage.
Our SmartBug technology automatically detects wheel flats, providing early alerts and trends; after detecting a 55mm flat, stakeholders were alerted, leading to the prompt turning of the wheel set.
Wheel pits are depressions or cavities on the wheel surface.
Stress Concentration: Wheel pits can act as stress concentrators, leading to a heightened risk of crack initiation and propagation.
Premature Wheel Wear: Pits can accelerate the wear of the wheel, reducing its lifespan and leading to increased maintenance and replacement costs.
Track Damage: Pits can lead to uneven wheel-rail contact, which might result in localised rail damage or wear over time.
Reduced Ride Comfort: Wheel pits can cause inconsistent wheel-rail interactions, leading to vibrations that affect passenger comfort.
Increased Inspection Need: Wheel pits necessitate more frequent inspections to ensure the wheel’s condition is safe for continued operation.
Solution: Our SmartBug technology detects early-stage wheel pits, alerting clients in time for preventative tyre turning instead of relying on mileage-based maintenance.
Rolling Contact Fatigue (RCF) is frequently a prevailing damage mechanism for wheel pans.
Our SmartBug technology detects RCF and ride quality issues early, providing alerts and trends. The graph demonstrates its effectiveness in alerting clients to RCF, allowing timely wheel set turning and extending wheel pan lifespan.
Infrastructure
Our technology is capable of recording impacts corresponding to track defects and pinpointing the location, allowing for infrastructure monitoring that measures exactly what a live train experiences.
General Detection
Bearing Issues
SmartBugs® can detect early signs of bearing issues by monitoring vibrations and temperature variations. Sudden increases in vibration levels or temperature can indicate potential bearing failures, allowing for timely maintenance to prevent costly downtime.
Wear of gearbox components such as gears and bearings can cause an increase in noise and vibration, and lead to premature failure of the drive-train.
Our SmartBug technology identifies early gearbox issues; the pictured example exceeded fleet average vibrations, prompting client inspection and repair.
Out Of Balance
SmartBugs® can detect out-of-balance conditions by analysing vibration data. Any deviations from the normal vibration signature can indicate imbalance issues, allowing for adjustments to be made to prevent further damage or wear.
Duty Cycle
SmartBugs® provide insights into the duty cycle of equipment by monitoring strain, vibration, and temperature changes during operation. This data helps in optimising maintenance schedules and ensuring that equipment is used within its designed duty cycle, increasing its lifespan.
Rail-Specific Detection
Wheel flats are localised flat spots on train wheels caused by prolonged skidding, leading to increased vibration, noise, and track damage.
Our SmartBug technology automatically detects wheel flats, providing early alerts and trends; after detecting a 55mm flat, stakeholders were alerted, leading to the prompt turning of the wheel set.
Wheel pits are depressions or cavities on the wheel surface.
Stress Concentration: Wheel pits can act as stress concentrators, leading to a heightened risk of crack initiation and propagation.
Premature Wheel Wear: Pits can accelerate the wear of the wheel, reducing its lifespan and leading to increased maintenance and replacement costs.
Track Damage: Pits can lead to uneven wheel-rail contact, which might result in localised rail damage or wear over time.
Reduced Ride Comfort: Wheel pits can cause inconsistent wheel-rail interactions, leading to vibrations that affect passenger comfort.
Increased Inspection Need: Wheel pits necessitate more frequent inspections to ensure the wheel’s condition is safe for continued operation.
Solution: Our SmartBug technology detects early-stage wheel pits, alerting clients in time for preventative tyre turning instead of relying on mileage-based maintenance.
Rolling Contact Fatigue (RCF) is frequently a prevailing damage mechanism for wheel pans.
Our SmartBug technology detects RCF and ride quality issues early, providing alerts and trends. The graph demonstrates its effectiveness in alerting clients to RCF, allowing timely wheel set turning and extending wheel pan lifespan.
Infrastructure
Our technology is capable of recording impacts corresponding to track defects and pinpointing the location, allowing for infrastructure monitoring that measures exactly what a live train experiences.
SmartBug® Customer Testimonials

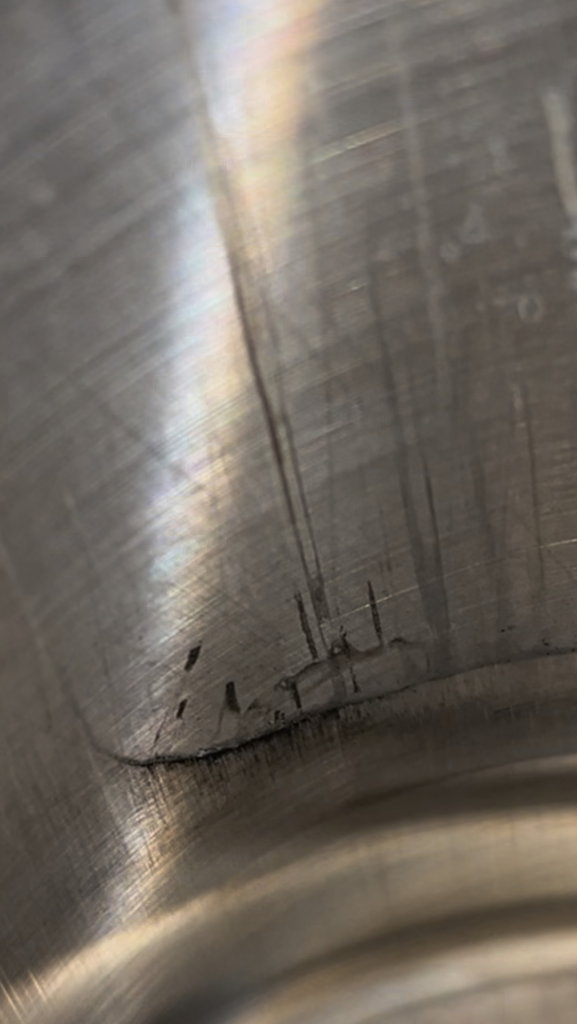
"Train has been pulled from service. It had an emergency brake which caused major flats. Good detection by the smart bugs as well."
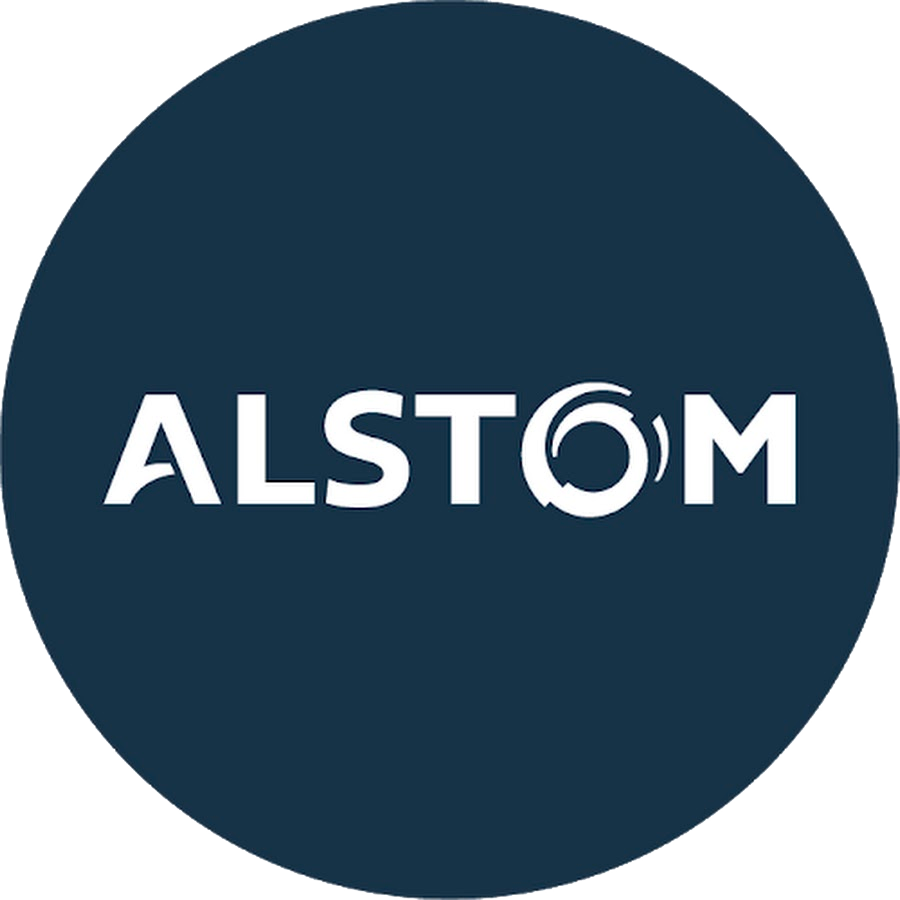
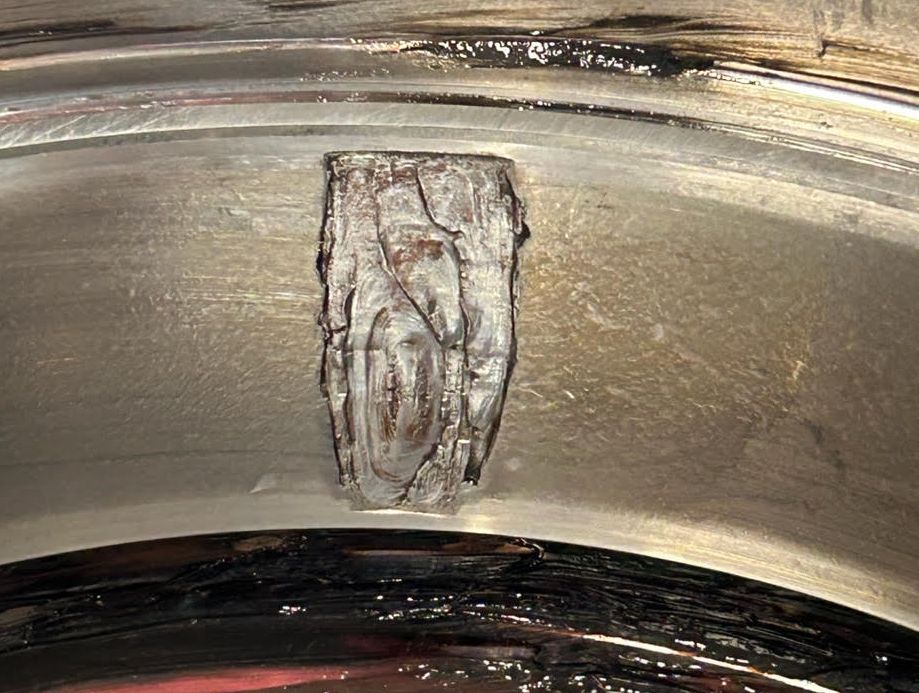
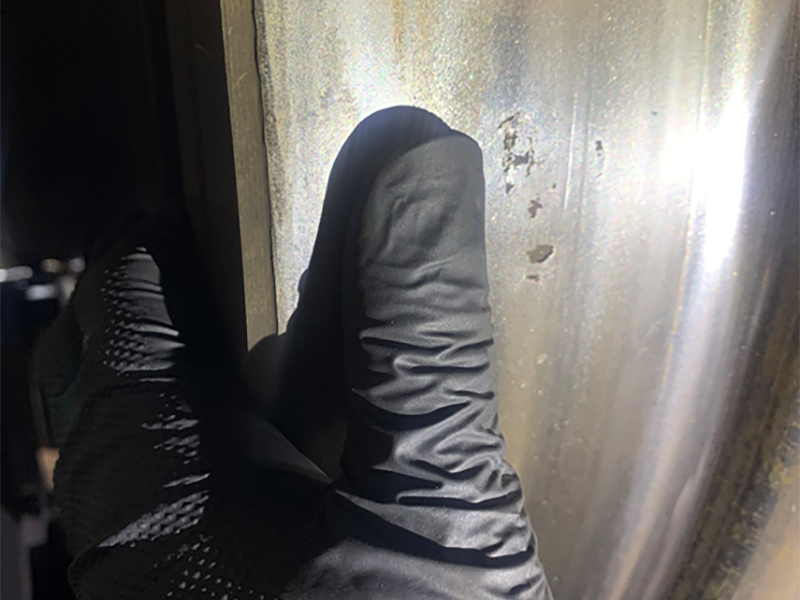
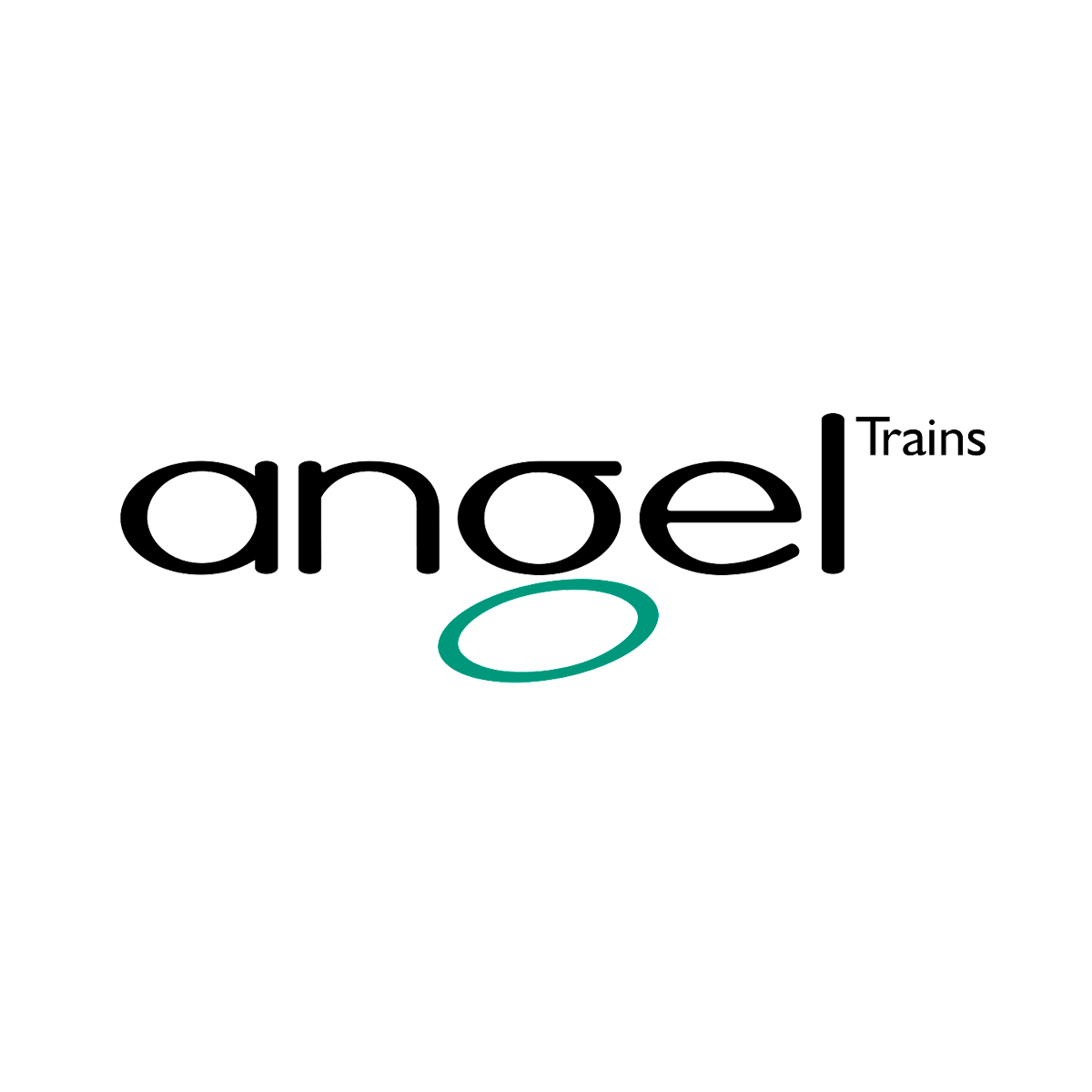
Set was examined last night and booked to go one journey only to [the depot] today to get the tyre turned.
On examination these flats were reported as 55 mm long, which is obviously out of traffic.”
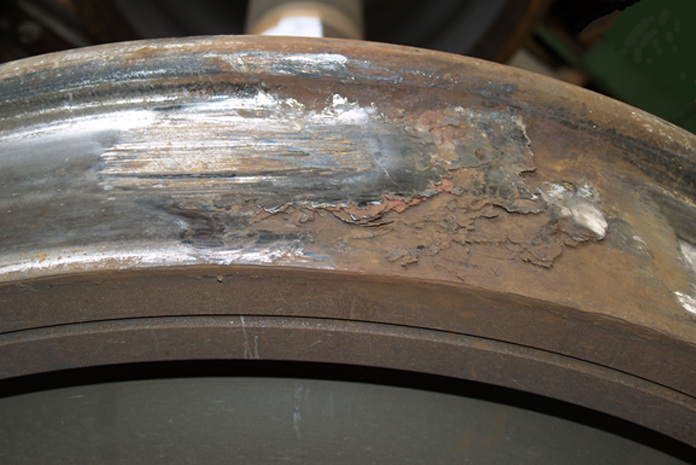
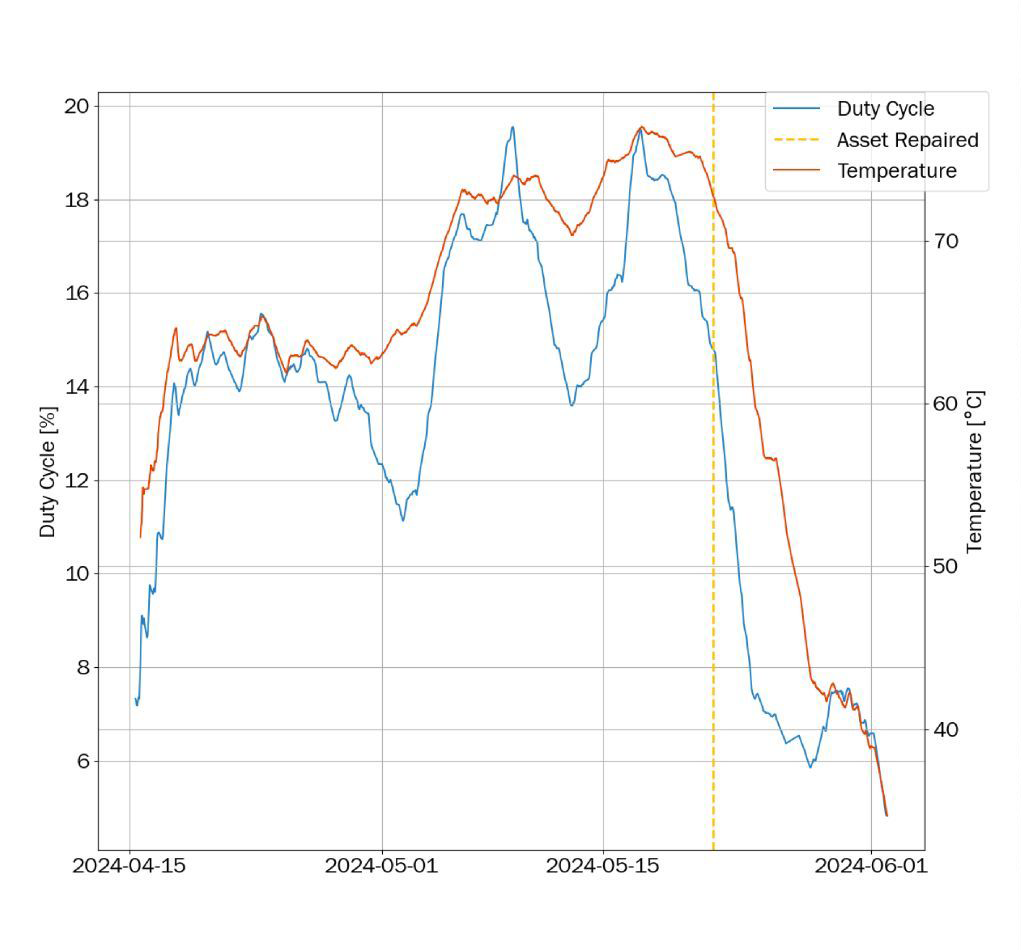
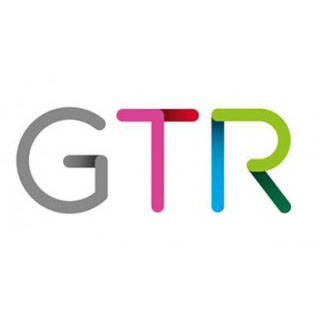
SmartBug® Wireless Sensor Technical Specifications
Learn more about Smartbug® Wireless Sensors on LinkedIn.
SmartBug® Compact Wireless Sensor
Big Performance in a Small Package
The SmartBug® stands out for its miniature dimensions, making it a versatile solution for a wide range of applications. Measuring a mere 28mm in diameter and 15mm in height, its compact wireless sensor design ensures it can be seamlessly integrated into diverse environments without occupying valuable space. This is particularly crucial in industries where space constraints are a challenge.
The significance of its small size lies in its ability to fit into tight spaces where larger sensors may not be practical. Whether it’s monitoring vibrations within machinery, vehicles, or infrastructure, the SmartBug® can be discreetly installed to provide critical data insights without impeding operations. Its compact profile also enables hassle-free installation in areas where accessibility is limited, ensuring comprehensive asset monitoring without compromise.
Moreover, the compact form factor of the SmartBug® enhances its portability, allowing for swift deployment across multiple locations as needed. Whether it’s monitoring temperature variations, analysing vibrations, or tracking movements, the SmartBug® offers unparalleled flexibility and ease of installation, thanks to its compact size.
In industries where every inch counts, the SmartBug® compact wireless sensor’s stature delivers big on performance, demonstrating its adaptability and efficiency in diverse operational settings.
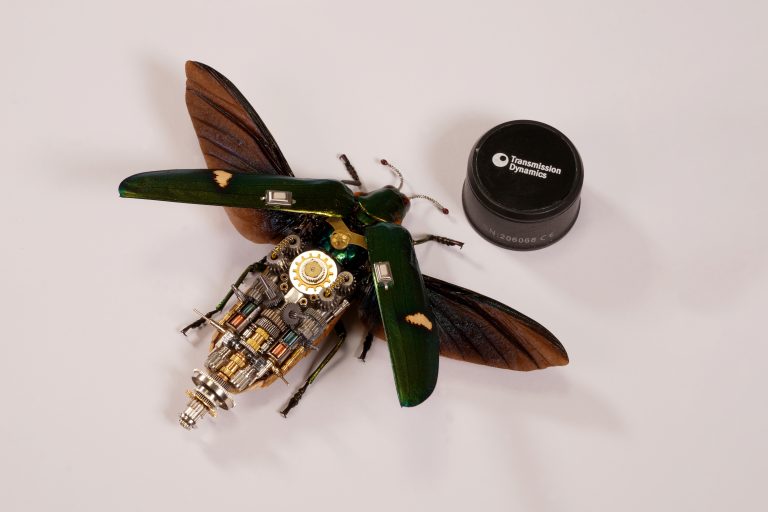
How our SmartBug® wireless sensor system achieves results via Data Analysis
By combining numerous analytics techniques using both human-derived engineering analytics, combined with Artificial Intelligence, the SmartBug® Wireless Temperature Sensor and Wireless Vibration Sensor is able to give unparalleled diagnostics information.
1. Initial Data Organisation
Baseline Deviations
This enables rapid identification of irregularities, streamlining the troubleshooting process and minimising downtime.
Threshold Alerts
Employing an intricate alert system, we proactively identify deviations from established thresholds.
Spectral Analysis
This sophisticated technique uncovers nuanced patterns that can hold crucial information about system behaviour and anomalies.
Data Trending
This perspective offers invaluable insights into long-term behaviour patterns and potential trajectories.
Fleet Analysis
This comprehensive view empowers strategic decision-making by providing insights into fleet-wide performance, trends, and optimisation opportunities.
Usage Monitoring
This scrutiny allows us to identify wear and usage-related trends, facilitating predictive maintenance strategies.
2. Data Filtering
Human-Derived Engineering Analytics
Beyond the realm of automation, our process incorporates the expertise of human-derived engineering analytics. Our skilled professionals interpret the data in tandem with their industry know-how, adding a layer of contextual understanding that enhances the accuracy of our insights.
Multi-layer Perceptrons and Neural Networks
Utilising cutting-edge technology, we employ multi-layer perceptrons and neural networks. These advanced algorithms possess the capability to discern intricate patterns within the data, allowing us to uncover hidden correlations and anomalies that might go unnoticed through traditional methods.
3. Real-time Outputs
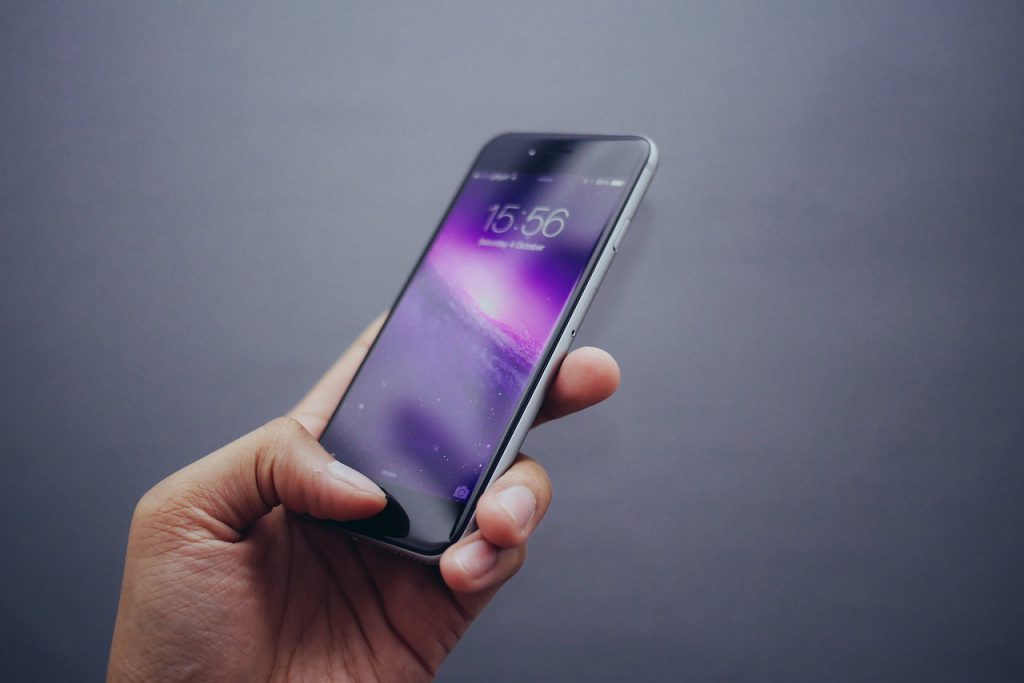
Real-time Alerts
Get immediate SMS and email notifications to respond promptly to critical situations.
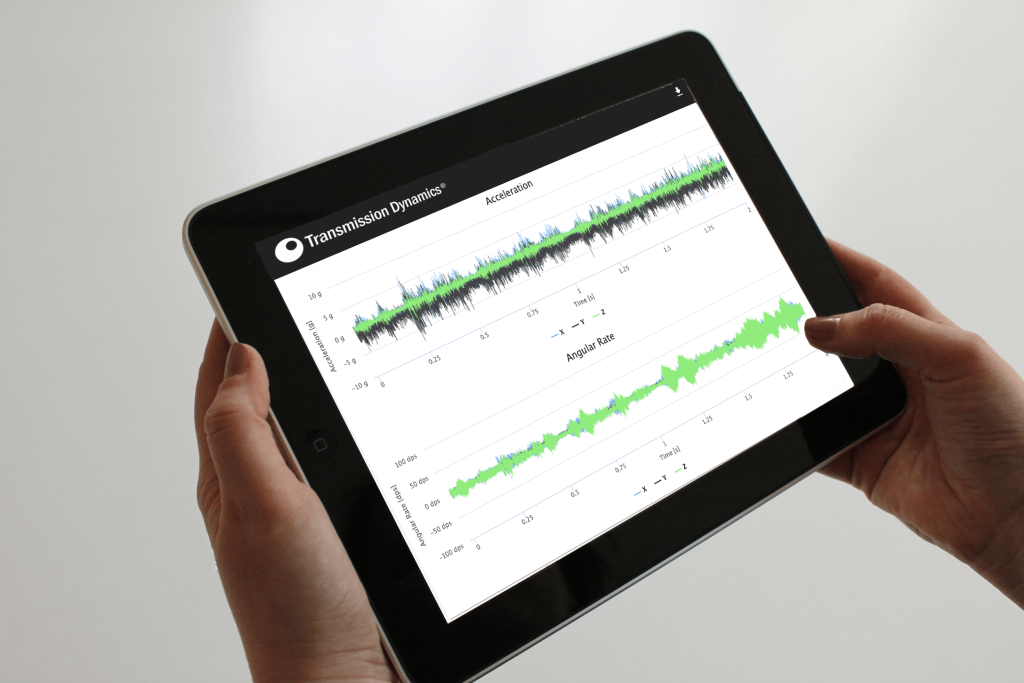
Asset Health Analysis
Explore in-depth asset health insights from advanced data analysis for informed decision-making.
Ease of Installation - Wireless Transmitter & Gateway
Transmitter Installation
CLEAN & GLUE
PRELOAD WITH MAGNETIC CLAMP
OPERATE SMARTBUG®
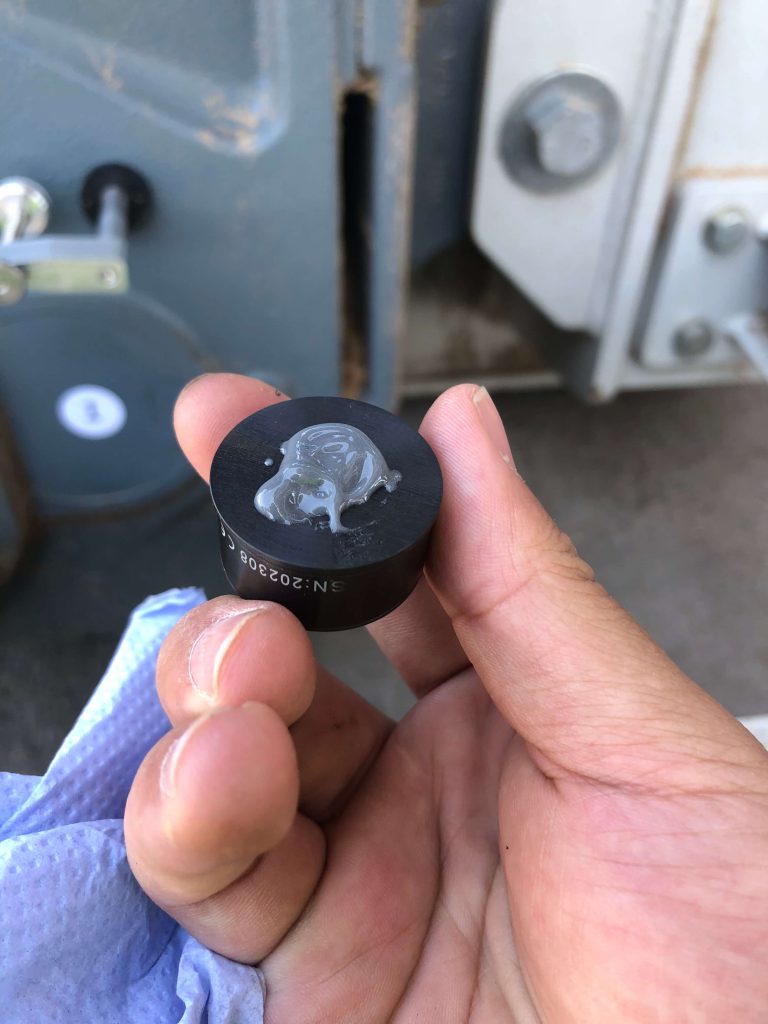
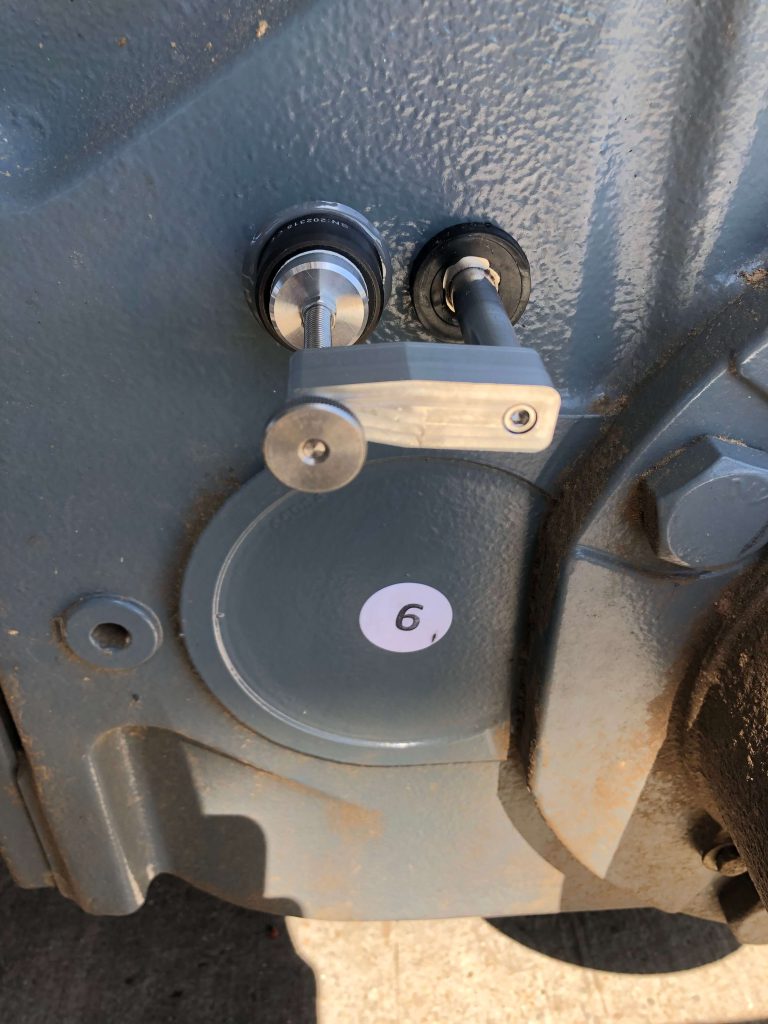
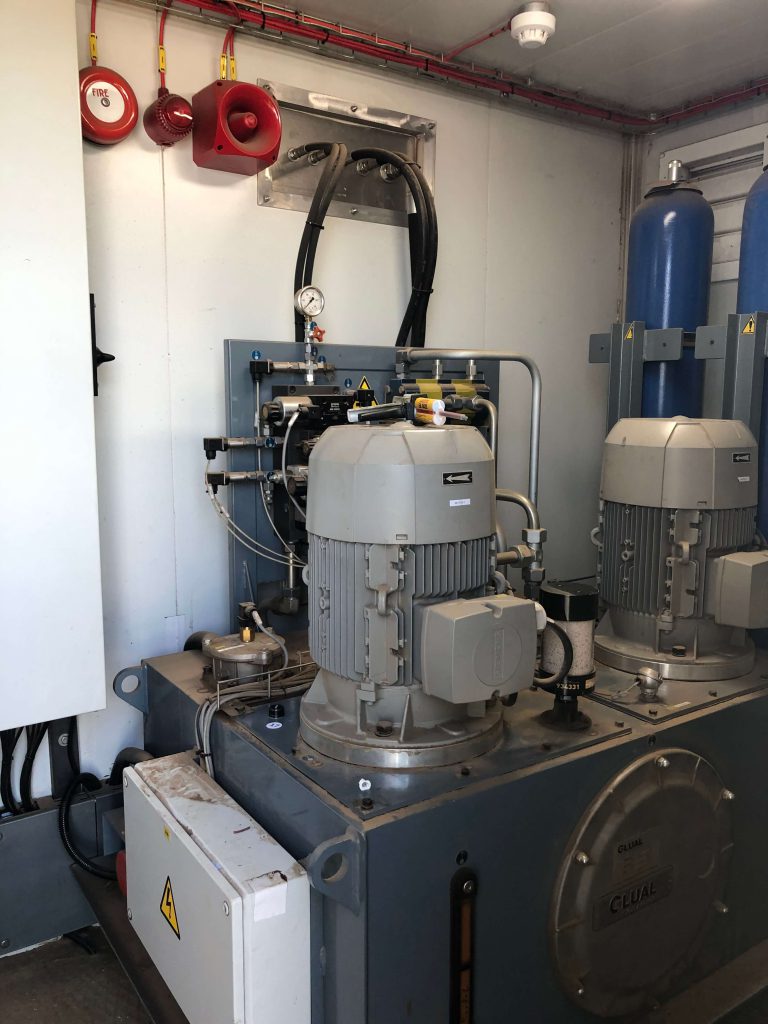
Gateway Installation
Insert SIM card
Supply Power
requires 24 V power
Remote system check
by our team at Transmission Dynamics
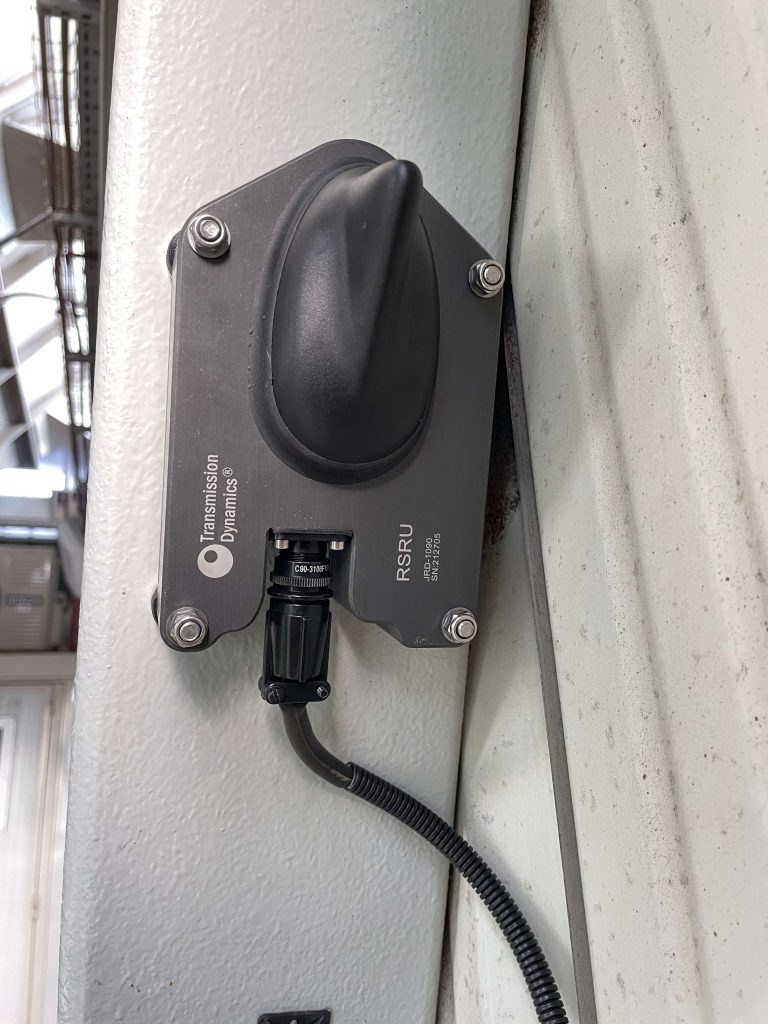
Part of the Transmission Dynamics Ecosystem
PANDAS-V®
This advanced system revolutionises rail industry practices by offering affordable and scalable remote condition monitoring solutions for electrified train pantographs and overhead lines. By addressing maintenance challenges and enhancing efficiency, PANDAS-V transforms rail operations and sets new standards for monitoring and maintenance in the industry.
Smart Oil Plug®
The Smart Oil Plug® is an innovative technology designed for the railroad industry, providing real-time monitoring of final drives and transmissions via wireless data transmission, detecting various parameters like temperature, vibrations, oil debris, and more, while offering extended maintenance intervals and global data access.
Want to know more about the SmartBug® experience?
Fill in the form and we will get back to you as soon as we can.