Bolts used in critical applications require frequent, precautionary maintenance regimes to ensure tension remains within the required range. This incurs significant operations and maintenance costs, increased downtime and safety risks. To address these challenges, Transmission Dynamics have embarked on an R&D project dealing with the ongoing issues with bolted joint integrity. This project, part-funded by the Offshore Wind Growth Partnership, aims to investigate the reasons for lost bolt tensions during installation, re-tightening, and standard wind turbine operations.
The use of hydraulic tensioners – do we get it right?
Hydraulic tensioners are commonly used to address bolt tightening requirements on critical fastenings in wind turbine applications. However, there is a fundamental problem with this approach. Hydraulic tensioners typically grip part of the available thread and apply tension to the bolt. Simultaneously, the nut is tightened manually to eliminate clearance. Once the required bolt tension is achieved and the nut cancelled axial clearance, there is a common belief that after removing hydraulic pressure, the bolt tensions will be retained. Commonly, this requires overcompensation for the known loss of tension which occurs as the hydraulic pressure is reduced.
Addressing common misconceptions
Transmission Dynamics’ engineers conducted a study at the Levenmouth demonstration turbine, where they installed six M64 bolts. A hydraulic tensioner was used in standard operation, alongside instrumented bolts equipped with BoltSense® LMF+ technology. Both sets of data were recorded simultaneously. Despite attempts to overcompensate for the target load of 1,680 kN, the instrumented bolts revealed under-tension as soon as the hydraulic pressure was released. This highlights the shortcomings of hydraulic tensioner methods. The results of this project will be disseminated globally to ensure critical aspects of bolted join integrity are properly handled and addressed.
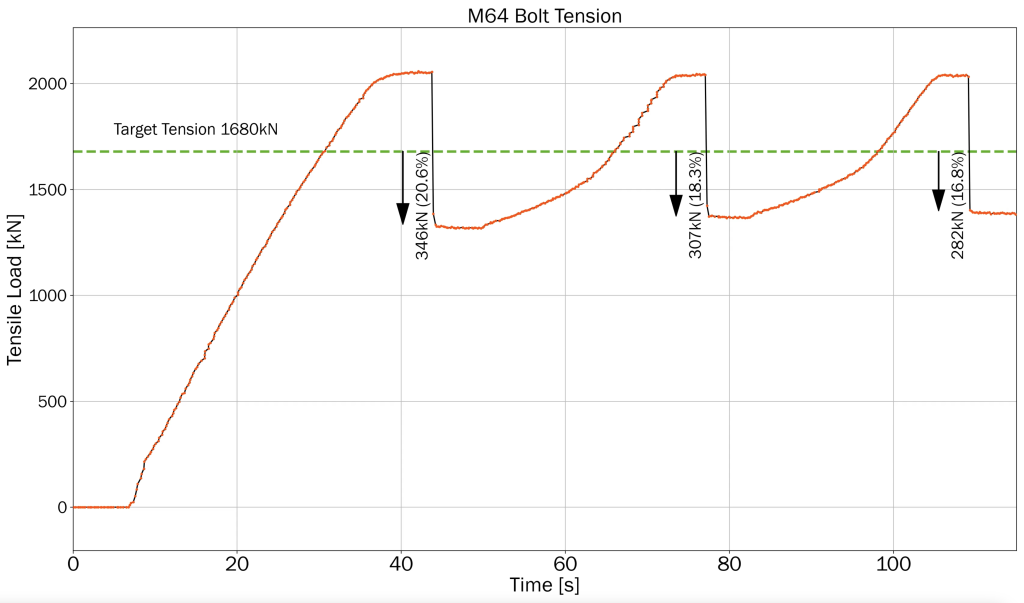
Advancements in Bolt Monitoring Technology
Transmission Dynamics, in partnership with Copper State Bolt and Nut Company, has developed BoltSense®, a powerful bolt monitoring technology. One aspect of this technology includes an automated calibration rig which is critical for high-volume calibration of industrial fasteners. The entire technology has been developed in-house, and it’s changing the global landscape in tension monitoring in critical fastener applications.