Wind with a Mind: Smart-Monitoring, Seamless Measuring
Wind Turbine Monitoring Solutions for Power Generation Instrumentation
Transmission Dynamics stands at the forefront of wireless industrial sensor solutions, exemplified by our award-winning engineering expertise in design, development, and deployment of wireless turbine condition monitoring.
Design & Load Validation
Turbine Condition Monitoring & Structural Health
Troubleshooting & Turbine Bolting Failures Investigation
The Wind Turbine Monitoring Instrumentation Possibilities are Endless...
At Transmission Dynamics, we integrate a diverse array of engineering disciplines, including mechanical, electronics, embedded systems, and data analytics, to provide precise and reliable measurements in turbine condition monitoring systems.
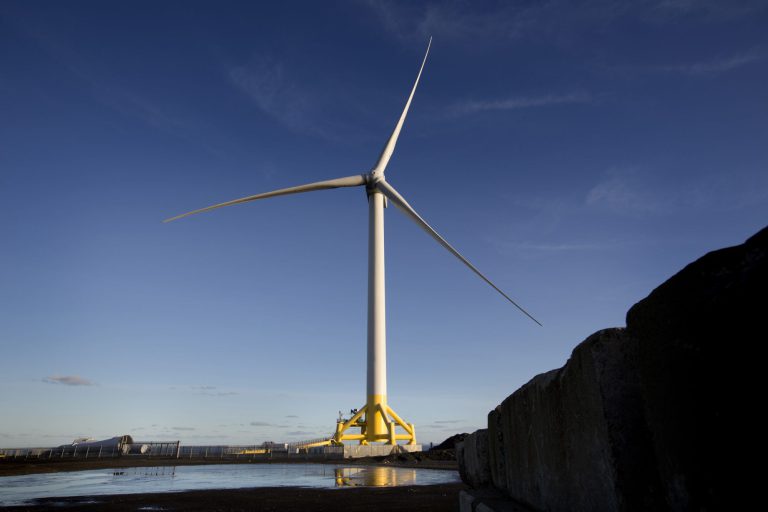
Your Partner in Optimal Sensor Placement
As the UK lead in the USA-UK Bilateral Collaboration Consortium, we played a central role in the Optimal Sensor Placement for Physics-Based Digital Twins project, driving forward the design and implementation of advanced wireless instrumentation in the power generation industry.
The project focussed on identifying optimal sensor placement for digital twinning technology to enable informed and optimised O&M planning and elimination of unnecessary precautionary inspections and interventions for the global offshore wind industry.
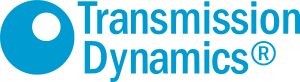
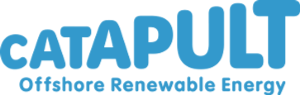
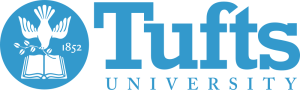
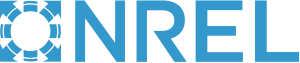
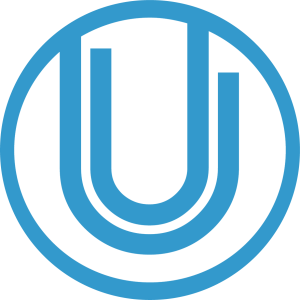
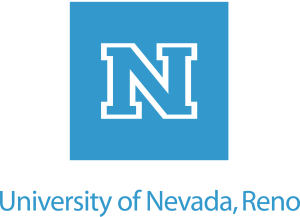
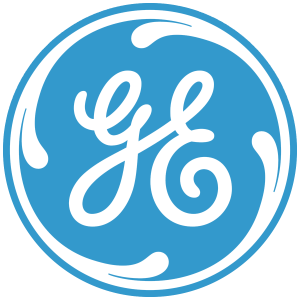
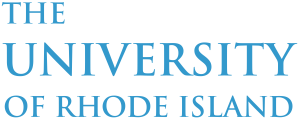
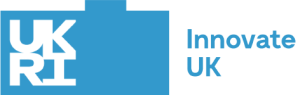
Extend the Lifespan of Your Aging Wind Assets with Smart Condition Monitoring
As wind turbines age, the challenge of maintaining reliability and performance grows—but so does the opportunity to extend their operational life. Transmission Dynamics provides advanced wind turbine monitoring solutions designed specifically for lifetime extension (LTE) programs, helping you maximise ROI on aging fleets while minimising unplanned downtime.
Why Monitor Aging Wind Turbines?
Early Fault Detection
Proactively identify wear, misalignment, and structural fatigue before failures occur.
Regulatory & Safety Compliance
Ensure aging turbines meet evolving industry standards with real-time health insights.
Reduce Maintenance Costs
Replace reactive repairs with data-driven interventions, cutting unnecessary inspections.
Optimise Asset Lifespan
Continuous monitoring ensures critical components (gearboxes, bolts, bearings) operate within safe limits, delaying costly replacements.
Effortless Installation, Persistent Monitoring
Our rugged wireless sensors install with minimal turbine modifications, provide decade-long reliability, and enable remote fleet health oversight - eliminating unnecessary and costly site visits.
Key LTE Monitoring Solutions
Structural Health Monitoring
Our products detect micro-cracks, stress fractures, and foundation shifts in aging towers and blades.
Gearbox & Bearing Degradation Tracking
Our systems pinpoint early-stage gear wear, preventing catastrophic failures.
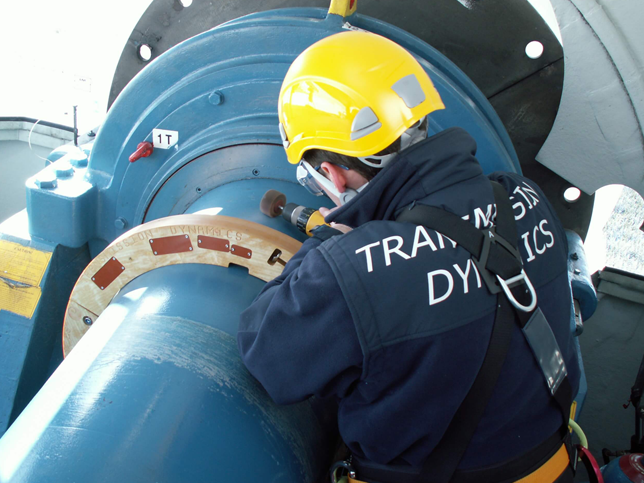
Bolt Tension Surveillance
Continuous monitoring prevents loosening in critical bolted joints - a major risk in older turbines.
Load Validation for Retrofits
Verify the impact of upgrades or life-extension modifications with precise strain and vibration data.
The LTE Advantage: Smarter Than "Run-to-Failure"
Many operators of aging turbines face a dilemma: replace or extend? With our wireless sensor networks and physics-based digital twin integration, you gain:
Predictive Maintenance
Move beyond calendar-based checks to condition-based strategies.
Fleet-Wide Insights
Compare performance trends across turbines to prioritise high-risk assets.
Retrofit Readiness
Validate the ROI of component upgrades with before/after performance analytics.
Next Steps for Your LTE Strategy
Whether you’re planning a 10-year life extension or mitigating risks in a 15+ year-old turbine, our bespoke monitoring systems deliver the data you need to decide with confidence.
Consult our experts and let us review your fleet’s LTE potential.
Lorem ipsum dolor sit amet, consectetur adipiscing elit. Ut elit tellus, luctus nec ullamcorper mattis, pulvinar dapibus leo.
Explore Our Wind Condition Monitoring Solutions
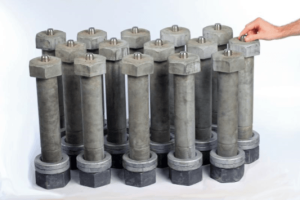
Tower Flange Load Monitoring Fasteners
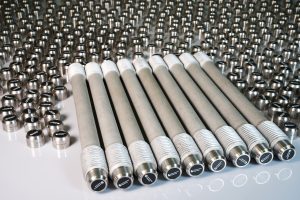
Blade Stud Load Monitoring
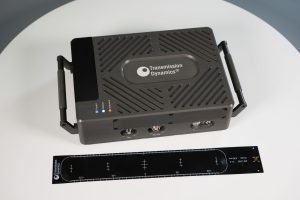
Tower & Jacket Ultrasonic SHM
Additional demonstrations of our power generation instrumentation, testing, and design capabilities are accessible through our Services page.
Wind Turbine Monitoring Services
Our team is adept at meticulous gearbox inspections, ensuring longevity and reliability of your turbine operations. Coupled with this, we specialise in noise and vibration measurements, employing state-of-the-art tools to assess and ensure the operational health of your power generation assets. Additionally, our expertise extends to turbine bolting failures and failure mode analysis, allowing us to pin-point the root of problems; enabling maximisation of uptime and efficiency of wind turbine condition monitoring.
Some of our Energy Sector Clients
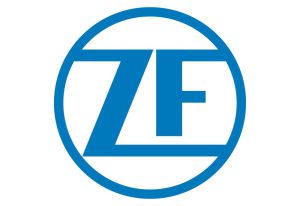
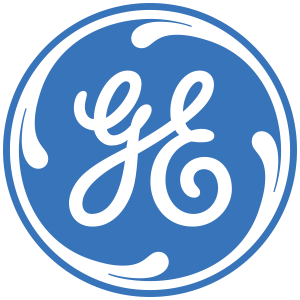
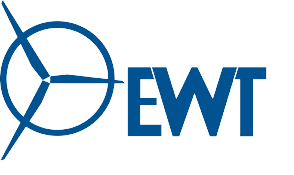

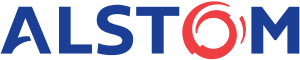
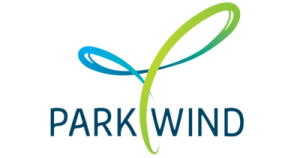
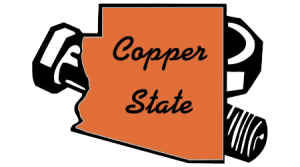

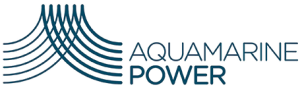
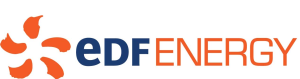
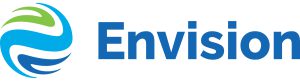
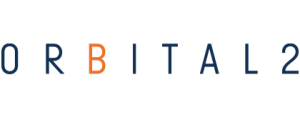
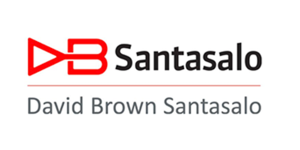
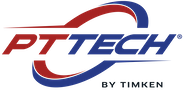
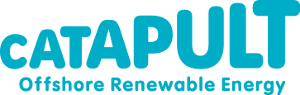
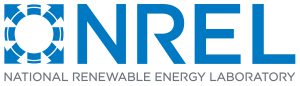
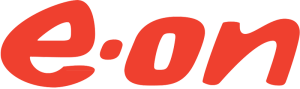
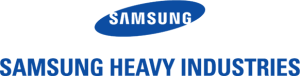
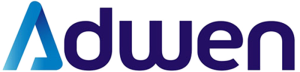
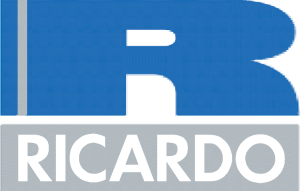
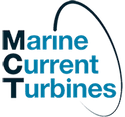
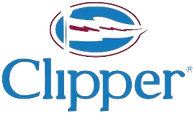
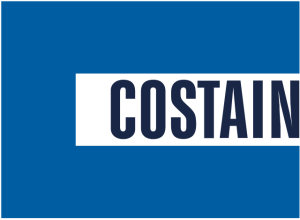
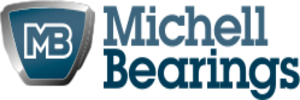
Gearbox Instrumentation
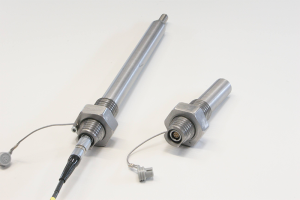
Plain Bearing Oil Thickness & Pressure
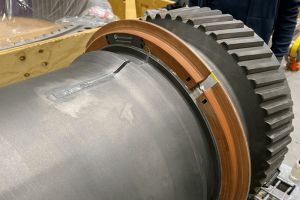
Torque & Bending Measurements
Tackling Wind Turbine Gearbox Challenges: A Comprehensive Analysis
Transmission Dynamics Chairman and Founder Jarek Rosinski along with David Smurthwaite delve into the complexities of preventing in-service failures in wind turbine gearboxes. As wind energy continues to surge, larger turbines pose new operational challenges, driving up costs and maintenance needs.
With a focus on gearbox dynamics, the authors explore critical factors influencing reliability and propose advanced monitoring techniques for enhanced performance and longevity.
Through a meticulous examination of real-world data, they underscore the significance of proactive maintenance strategies and collaborative industry efforts in ensuring the sustainability of power generation instrumentation in wind energy.
Please click the image to view a PDF of the article, which opens in a new window/tab.
Understanding the importance of Bolt Tension in Wind Turbine Integrity
Engineering projects worldwide rely on critical bolting applications for safety and efficiency. Bolt failures present a significant challenge, particularly in the wind energy sector, where accurate and continuous data on bolt tensions is crucial to prevent incidents. Hydraulic tensioners used in wind turbines encounter fundamental difficulties in achieving correct bolt tensions, leading to potential safety risks as many wind turbine bolts are not installed to specified preload.
Moreover, bolt tensions are typically checked only every 6 months, allowing for potential loosening in between. Recognising these challenges, Transmission Dynamics Technology offers live wind turbine condition monitoring for immediate and effective addressing of turbine bolting failures, incorporating power generation instrumentation for comprehensive insights into operational performance.
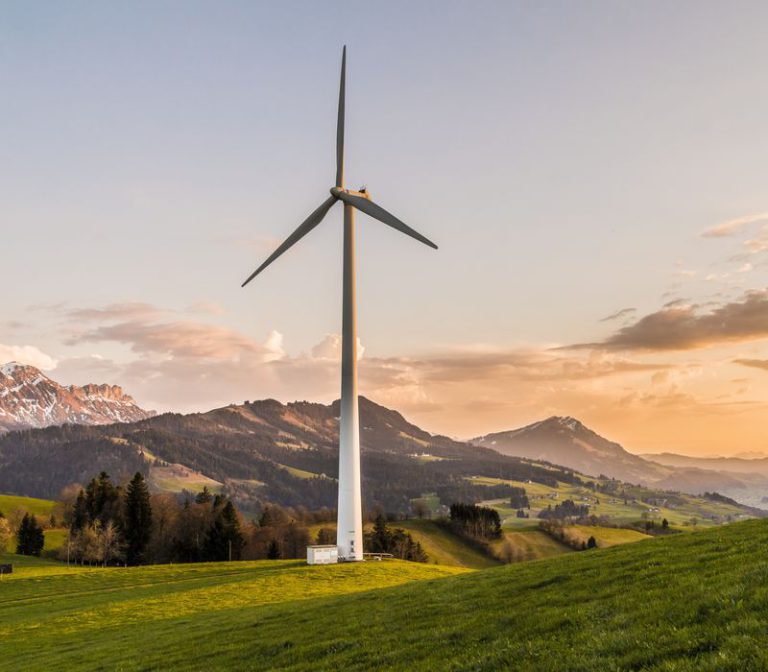
Unleash the power of cutting-edge solutions from Transmission Dynamics.
Discover Transmission Dynamics’ cutting-edge technologies tailored to elevate your operations. From wind turbine monitoring systems to wireless telemetry solutions, we deliver unparalleled performance, reliability, and cost-effectiveness. Our expertise in providing real-time data insights and power generation instrumentation empowers your business to make informed decisions and optimise performance.